Quality you can trust
Our manufacturing facility is based here in the United States, guaranteeing our clients the reliability, timeliness, and quality they need. And with our broad range of manufacturing capabilities, we have the flexibility to accommodate your exact needs. If you’re looking for a cost-effective, reliable, and quality-assured medical device contract manufacturing partner, you’ve come to the right place.
Carbon Fiber
Light-weight, high-strength, and radiolucent, carbon fiber is an ideal material for a variety of patient positioning products.
To put this strength into perspective, a recent carbon fiber positioning product we created is able to hold 1250 pounds. The weight of the product itself? Only 11 pounds!
When manufacturing with carbon fiber, our engineers use carbon fiber fabrics pre-impregnated with epoxy resin to create the ideal binding matrix. Depending on the customer's needs, we’re also able to incorporate core materials, such as rigid foam to optimize product performance.
Our carbon fiber processing capabilities include:
- Design & Engineering know-how to balance product specs with application needs
- In-house tooling design and build
- Steam-sterilization-compatible material options
- Freezer storage for raw material preservation
- CNC cutting operations for repeatable patterns
- Environmental controlled production area to promote material stability
- 3.9’ (1.2 meter) x 14’ (4.3 meter) autoclave with programmable cycles and computerized cycle tracking
Compression Molding
Achieve durable, fluid-resistant positioning surfaces with compression molded textured ultra-foam (“TUF”) finishes. Utilizing in-house machined and finished molds we have a variety of press sizes to efficiently achieve TUF products utilizing closed cell foam substrates. We can also bond a variety of healthcare fabrics (“HCF”) to the closed-cell foam substrate to provide an attractive option for patient contact surfaces.
The individual sheets of closed-cell foams are typically less than 3” thick. We have a variety of lamination and welding options to produce products that are substantially larger than the available sheets. We can also achieve thinner profiles using foam skiving to prepare thin sheets for molding.
With press sizes up to 8’ x 12’, Domico Med-Device can compression mold virtually any size or shape you need.
Product Assembly
Our design, engineering, and production capabilities, here at Domico Med-Device, culminate with the final assembly and testing of mechanical and electromechanical devices. Built to exact specifications, we carefully construct products to meet the requirements of the medical device industry.
The same care is given to contract manufactured systems, such as MRI coils, CT scanners, and ceiling mounted accessory suspension systems
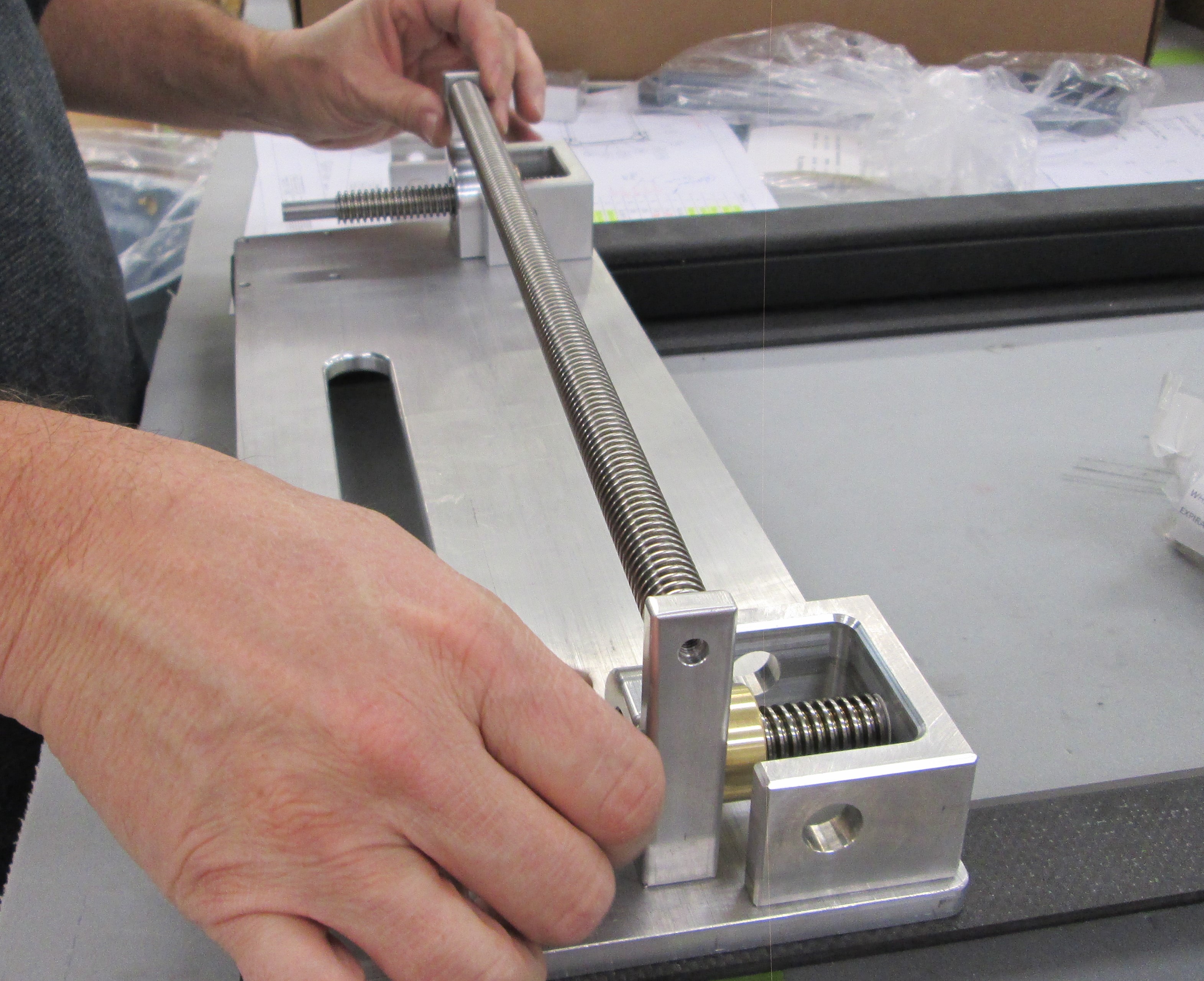
Foam Fabrication
Foam fabrication continues to be a key driver in our success. With decades of experience, we can help you select optimal materials and processes to fit your application. Using advanced techniques with the highest quality in mind, our capabilities are geared to produce virtually any shape or size, whether you need one piece or thousands.
Our foam fabrication equipment includes:
- Large format band saws for blanking and staging
- CNC reciprocating and band saws for accurate, high-speed cutting
- Skiving saws for automated slicing of thin sheets of rigid or flexible foams
- Lamination and welding, of multiple layers of foam or dissimilar materials, to achieve integral bonds
- Compression cutting: a hydraulic press forces foam through a pattern, then a saw blade slices the foam. The result is a concave or scoop cut that is ideal for cradles or holders.
Sewing
With years of experience and an eye for detail, we ensure quality is stitched into every seam. Processing a wide variety of fabrics and films, our skilled sewing team produces a broad range of products and accessories, including security straps, fabric covers, and assemblies. With our diverse background, there are few sewing needs that we can’t address.
Sealing
Domico Med-Device offers a variety of sealing techniques designed to create contamination resistant barriers without using adhesive. Each method involves heat, pressure, and time. Various sealing technologies can be used to suit your needs, depending upon the requirements of the materials or product design.
- RF sealing is the process of fusing together thermoplastic material using high frequency electromagnetic energy.
- Heat sealing is the process of using a heated tool to apply pressure and heat to form a bond between two or more layers of plastic.
- Ultrasonic sealing involves holding plastics or materials with dissimilar properties under pressure and locally applying ultrasonic acoustic vibrations to form an integral bond between the materials.
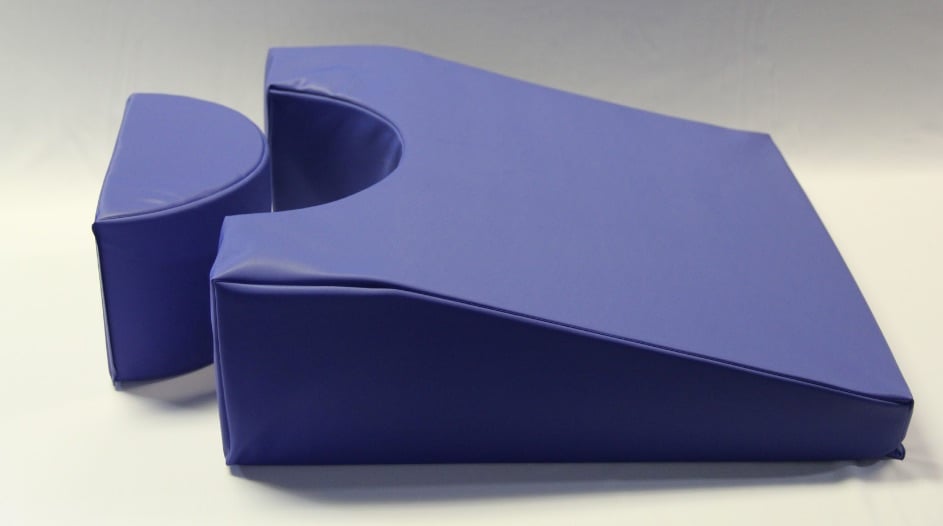
Coating
We can help you extend the life of your foam positioning aids with vinyl coatings. We achieve this by converting a porous foam substrate into a fluid, stain-resistant product. It all starts in our central paint kitchen, which houses a variety of materials and colors that are constantly agitated to maintain consistent viscosity.
The material is piped directly to the operator for product application. For small-volume applications, individual pressure pots are maintained to allow for efficient processing of unique colors.
When the specification calls for a carbon fiber or metal substrate, we use epoxy or urethane paints to provide Class A surface finishes. Our process controls, combined with skilled operators, create quality, repeatable finishes.
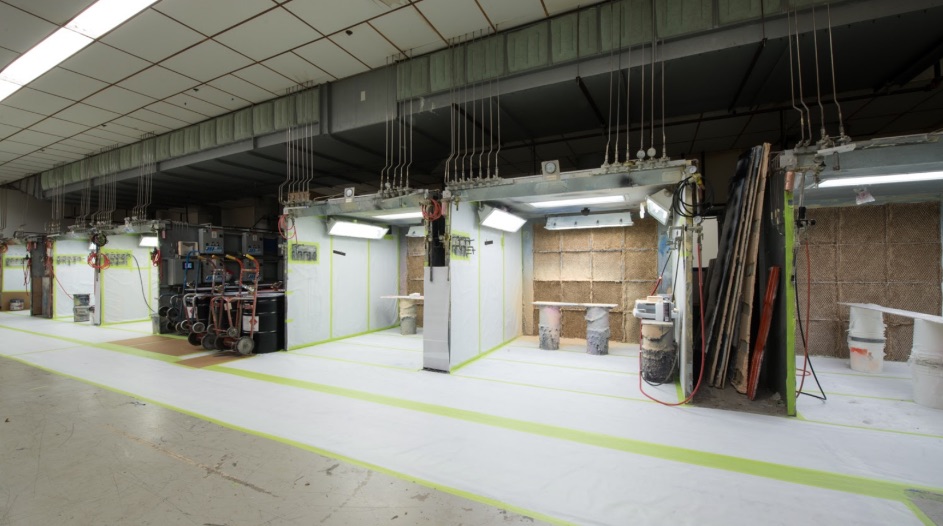
Vacuum forming
Vacuum forming begins with materials selection. Depending on the strength or imaging modality requirements, we can assist with the material choice to achieve the desired performance. Available in a variety of colors, textures, and thicknesses, we maintain an inventory of several thermoplastic sheets such as ABS, Kydex, and polycarbonate. We have access to a wide variety of materials should an application introduce a different requirement. Once the material is selected, the team uses our machining capability to craft a mold from the appropriate material, depending on your anticipated volumes. Aluminum, rigid urethane, or even wood can be optimal, depending on your needs.
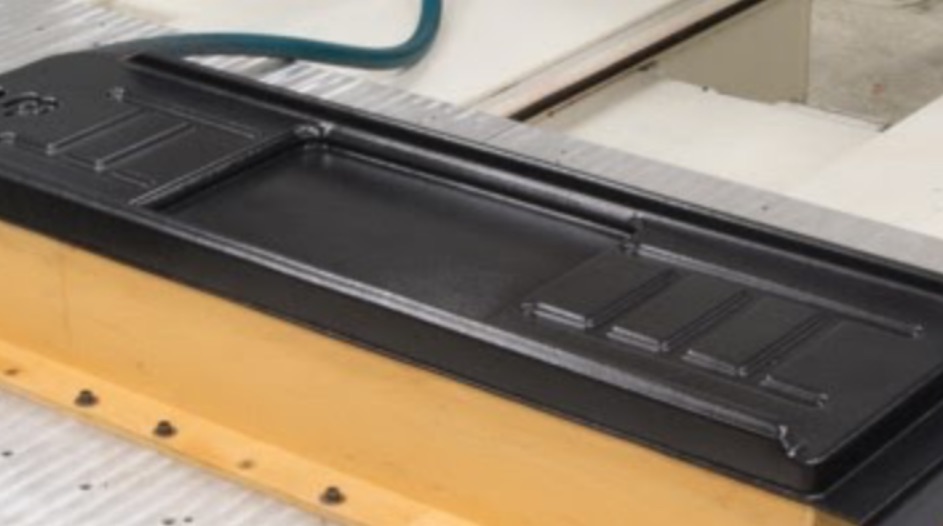
Machining, tool design and build
Whether you need a one-time custom tool or repeat production runs, we ensure precision and quality are cut into every machined detail, tool, and assembly. We use CAM software to efficiently convert CAD to cutting programs, and have robust machining and turning centers.
We’ll work with you when selecting materials to suit your product needs. Steel, aluminum, titanium, carbon fiber, foam, and plastic are a few of the materials that are routinely processed in our Machine Shop. We use local sources for metal treatments, such as anodizing, plating, and powder coating.
In-house equipment:
- Breton - 3-axis CNC milling center
- Hardinge - 3-axis CNC milling center
- YCM - 5' x 10' large format 3-axis CNC milling center
- Hurco - 5-axis CNC milling center
- Quintax - 5-axis CNC router w/dual vacuum tables
- Okuma - 7-axis lathe
- Bridgeport - vertical mill (2)
- Miltronics - CNC lathe
Printing & Marking
We have several in-house printing and marking capabilities that can be applied to your products or packages to maximize brand awareness with each product sale. Our printing capabilities include:
- Screen Printing. Apply your brand to large format products with silk screening. We often apply screen prints to foam pads, coated products, plastic films, and fabrics.
- Laser Engraving. With minimal set-up time, laser engraving is ideal for applying your brand to metal and thermal plastic substrates. The accuracy of the laser promotes repeatable, professional images.
- Thermal Transfer Printing. Easily identify or brand pouches, bags, and boxes with labels that are rapidly printed in low and high volumes. This is ideal for UDI compliant bar coding; the adhesives, papers, and inks have been validated for the rigors of medical device distribution.
- Laser Printing. High volume, high quality printing for black & white or color manuals, brochures, and inserts; can be custom printed to meet your specifications.
- Private Labeling. Apply your brand name, company logo, re-order information, and barcode to a wide range of products and packages. Our document control system will ensure the correct revision of your label is applied each production run.
.jpg)
Our capabilities, your customers’ benefit
If you would like to learn more about how Domico Med-Device can work with you to produce world-class medical devices, we’re always available to chat.